Ventilazione del locale di carica carrelli elevatori
Una guida alla ventilazione dei locali per evitare il pericolo di esplosione dovuto alla ricarica delle batterie
In ambito industriale è ormai consolidato l’uso di carrelli elevatori elettrici. Queste macchine sono corredate di un gruppo batterie ricaricabili che forniscono l’energia necessaria al corretto funzionamento dell’apparecchiatura. Le batterie utilizzate vengono comunemente definite “batterie per trazione”.
Com’è noto durante la fase di ricarica le batterie emettono gas tra cui l’idrogeno. Se la concentrazione in aria dell’idrogeno raggiunge il 4%, la miscela idrogeno-aria può esplodere; le norme EN 50272-2 ed EN 50272-3 prevedono che la concentrazione di idrogeno sia mantenuta significativamente al di sotto della suddetta soglia attraverso un’idonea ventilazione.
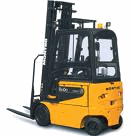
Ventilazione
Le norme EN 50272-2 ed EN 50273 indicano quale sia la corretta ventilazione per garantire la concentrazione di idrogeno al di sotto del 4%. La portata d’aria di ventilazione si calcola con la seguente formula:
Q = 0,05 * n * Igas * Crt / 1000
dove
Q = portata d’aria [mc/h]
n = numero elementi della batteria
Igas = corrente che produce gas [mA / Ah]
Crt = capacità nominale della batteria [Ah]
Da un punto di vista teorico il problema della ventilazione presenta a questo punto una facile soluzione: è sufficiente richiedere al costruttore del carrello elevatore le caratteristiche del pacco batterie e svolgere il semplice calcolo. Praticamente il problema è più complesso in quanto:
- i dati relativi alle batterie di accumulatori non sono reperibili a catalogo del carrello elevatore
- il costruttore del carrello elevatore molte volte non dispone direttamente dei dati delle batterie essendo in pratica un semplice assemblatore di queste
- le caratteristiche del pacco batterie cambiano a seconda della marca del carrello elevatore adottato e generalmente questa non è già univocamente definita in fase di progettazione
- i dati relativi a carrelli esistenti e/o di seconda mano sono difficilmente reperibili
Nel seguito cercheremo di svolgere un’analisi che con una serie di approssimazioni successive a favore della sicurezza riconduca ad un risultato leggermente sovradimensionato ma praticamente sempre corretto.
Nel caso di batterie da trazione aperte al piombo il termine Igas, salvo diverse indicazioni del costruttore, può essere assunto pari a 60 (norme EN 50272-2 ed EN 50273).
Restano da determinare il numero di elementi e la loro capacità. Per la determinazione di questi due parametri sono necessarie alcune considerazioni a priori che svolgeremo nel seguito.
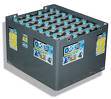
L’energia necessaria al corretto funzionamento del carrello elevatore è contenuta all’interno della batteria di accumulatori. Quest’energia è data dal prodotto della capacità della batteria per la sua tensione nominale di funzionamento e può essere espressa in VAh (oppure in kVAh) – vedi anche http://it.wikipedia.org/wiki/Batteria_%28chimica%29.
Si può ragionevolmente approssimare (e questo dato è confortato dai data sheet di molti costruttori di carrelli elevatori) che indicativamente ogni kg di portata del carrello elevatore sono necessari 20 VAh. Va da sé che è molto più semplice reperire la portata di un carrello elevatore che non i dati relativi alla sua batteria.
Inoltre le batterie da trazione comunemente usate per i carrelli elevatori sono costituite da elementi di tensione nominale 2V; a favore della sicurezza possiamo considerare la capacità di ciascun elemento pari a 100Ah (potrebbe anche essere anche maggiore ma se così fosse la ventilazione necessaria sarebbe comunque minore di quella considerata per elementi 100 Ah). Avremo pertanto che ogni elemento può “erogare” un energia pari a 200 VAh.
Sulla base di quanto sopra esposto, possiamo quindi affermare che ogni 10 kg di portata è necessario un elemento che presenta le seguenti caratteristiche:
– tensione nominale 2V
– capacità 100 Ah
In numero di elementi sarà pertanto determinabile dividendo la portata del carrello espressa in kg per 10.
Ritornando alla formula
Q = 0,05 * n * Igas * Crt / 1000
Avremo
Igas = 60
n = portata [kg] / 10
Crt = 100 Ah
Pertanto, effettuati tutti i passaggi matematici del caso che per brevità vengono tralasciati, avremo semplicemente che
Q = 0,03 * portata
Ricordandosi che Q è espresso in mc/h e la portata in kg (che corrisponde in pratica ad una ventilazione di 30 mc/h ogni 1.000 kg di portata).
La norma ci dice anche quanto devono essere ampie le superfici di aerazione in grado di garantire la portata d’aria necessaria e cioè:
A = 28 * Q
Dove
A = sezione netta delle aperture di ventilazione (cm2)
Q = portata d’aria richiesta (mc/h)
Per quanto riguarda la disposizione e la tipologia delle aperture di ventilazione rimandiamo a quanto indicato sulla guida relativa alla ventilazione naturale dei gruppi elettrogeni in quanto valgono le stesse considerazioni ( vedi )
Qualora non fosse possibile garantire la ventilazione richiesta mediante semplici aperture si può ricorrere ad un’estrazione forzata. E’ tuttavia necessario dotare il locale di un sistema automatico di controllo della corretta ventilazione (flussometro o relè amperometrico sul circuito di alimentazione del ventilatore); qualora questa venisse a mancare dovrà essere automaticamente interrotto il processo di ricarica delle batterie ed inviato un allarme agli operatori.
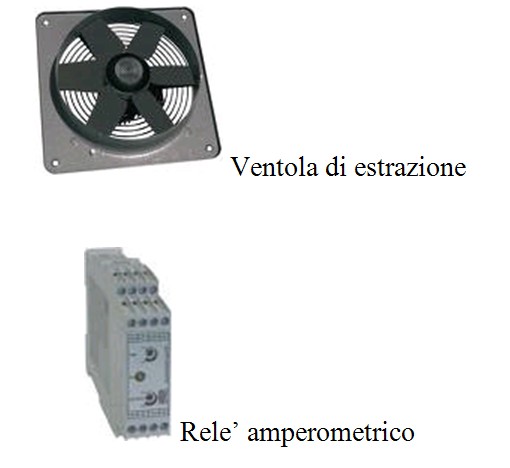
Esempio
Consideriamo un carrello elevatore portata 1200 kg equipaggiato con batteria 24V 800 Ah (dati desunti dal datasheet di una primaria casa costruttrice). Come si evince il numero di elementi della batteria non è indicato. Sono tuttavia indicate la tensione della batteria e la sua capacità che ci indicano un’energia contenuta pari a 19.200 VAh. Se avessimo usato il dato approssimato (20 VAh ogni kg di portata) avremmo ottenuto un’energia di 24.000 VA (25% di errore a favore della sicurezza). A questo punto possiamo effettuare i calcoli con l’energia esatta oppure utilizzare, a favore della sicurezza, la formula approssimata ricavata in precedenza.
Utilizzando la formula approssimata abbiamo
Q = 0,03 * 1200 kg = 36 mc/h
E pertanto
A = 28 * 36 mc/h = 1008 cm2
Sono pertanto necessarie 2 aperture (una di espulsione ed una di ripresa) di dimensioni indicative 60 x 20 cm (le dimensioni tengono conto della superficie occupata dalle griglie).
Qualora si avesse a che fare con più carrelli elevatori la portata d’aria necessaria totale sarà data dalla somma delle singole portate necessarie per ciascun carrello.
Distanza di sicurezza dalla batteria Evidenziamo infine che la norma EN 50272-3 considera come zona 1 (vedi classificazione Atex) il volume compreso entro una distanza di 50 cm dalla batteria. E’ pertanto necessario, per poter realizzare impianti “normali”, non installare componenti a meno di mezzo metro dalla batteria del carrello elevatore.
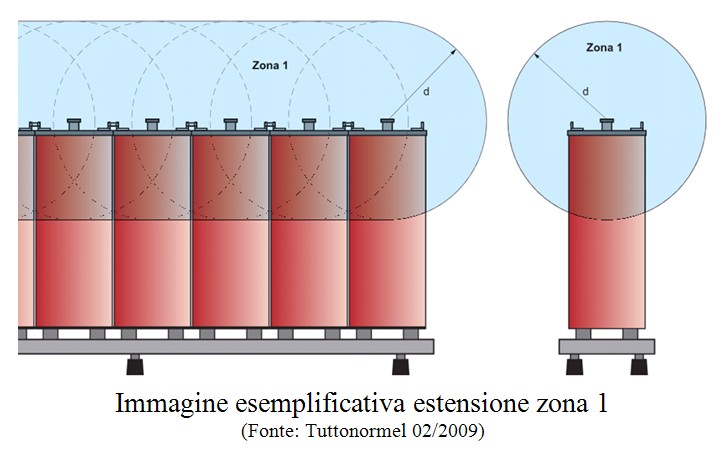
Conclusioni
Esprimiamo alcune considerazioni finali:
– le analisi sopra sviluppate rappresentano unicamente un punto di partenza per la determinazione della ventilazione dei locali in fase di progettazione e non possono sostituire i calcoli esatti che dovranno essere opportunamente svolti una volta noti tutti i dati necessari indicati dalla vigente normativa
– qualora sia possibile è opportuno prevedere il locale di ricarica carrelli all’esterno in modo da evitare tutte le problematiche sopraesposte
– il buon senso dice che dovrebbe essere il costruttore del carrello elevatore a comunicare la ventilazione necessaria per la ricarica del suo prodotto, ma purtroppo molto spesso realtà e buon senso non coincidono.